Innovative projects
Various research assignments and ongoing projects increase our performance towards our customers.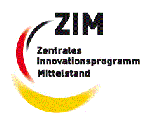
Ceraform
Die casting is ideally suited for the economically efficient serial production of components with complex geometries. This technology is not limited only to aluminium and magnesium, but may also extend to copper. Because of the necessary temperatures of over 1000°C, which are required for copper alloys, even highly alloyed steel grades suited for high temperatures cannot be used in a permanent manner. In addition to the high temperatures, the process requires also high pressures in excess of 1000 bar. This significantly reduces the service life of system parts and moulds.
Silicon nitride is already used today for various applications in aluminium foundries because of its excellent thermal shock resistance and corrosion resistance. Because of the increasing requirements applying to copper die-casting, QSIL Ingenieurkeramik GmbH (QSIL), together with its project partners, is developing optimized materials and processes that are necessary in order to enable economical large-scale use.
The research work described was funded through the Central Innovation Program for SMEs (ZIM), run by the German Federal Ministry of Economics and Technology (BMWi).
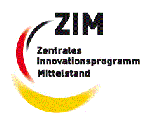
Nitride crystal
Carrier substrates made of monocrystalline aluminium nitride (AlN) are ideal for the deposition of semiconducting (AlGaIn) N-layers, which are used, among other things, as a basis for powerful and long-lasting UV light and laser diodes. The great advantages of these components have so far not come into play, however, since single-crystal AlN wafers have so far only been produced through a very complex process and at a high costs at research institutes for their own use. The main reason for this is the lack of a suitable high-temperature and corrosion-resistant crucible material, which would meet both the demanding requirements of the AlN single crystal growth process and the economic requirements. In the project, therefore, QSIL Ingenieurkeramik GmbH are working together with the Leibniz Institute for Crystal Growth in Berlin on the development of refractory ceramic materials and composite materials as well as of the high-temperature compression techniques necessary for the production, with the aim of developing usable crucible materials and components for the industrial production of single-crystal AlN wafers.
The research work described was funded through the Central Innovation Program for SMEs (ZIM), run by the German Federal Ministry of Economics and Technology (BMWi).
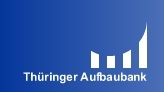
Paper ceramics
In recent times it has become possible to incorporate ceramic powders into paper as fillers. Starting from these pre-ceramic papers, structures may then be produced via paper-related processes, which are then in turn sintered to form corresponding ceramic structures. This way, light and at the same time rigid structures may be produced out of ceramics through well known processes, such as that involved in the production of corrugated cardboard.
While there are already the first commercial products in the field of oxide ceramics (see WZR ceramic solutions), the potential of non-oxide ceramics has not yet been exploited.
Therefore, QSIL Ingenieurkeramik GmbH and its partners develop lightweight and highly rigid structures made of non-oxide ceramic “papers” that, with their excellent thermal shock resistance and temperature resistance, are going to help make technical processes cleaner, less prone to contamination, more energy-saving and more efficient.
Rolicer
Due to their high abrasion resistance, fracture toughness, high temperature strength and chemical resistance, Si3N4 ceramics are particularly suitable as rolling elements for bearing applications and as rollers for the hot forming of semi-finished metallic products. Nevertheless, with particularly high mechanical and tribological loads or forming temperatures, there are still problems with regard to the reliability and service life of the rolling bearing or hot-rolling device component.
The “RoLiCer” research project therefore aims to optimize Si3N4 ceramics for rolling cylinders and rolling-element bearings, with a special focus on the optimization of the application-specific characteristics and on the development of models and calculation methods that enable concrete predictions of the reliability and service life in each application case. Furthermore, simulation work, as well as the examination of material samples and load tests under application conditions, will help gain fundamental knowledge about material failure and crack propagation, depending on the material structure and conditions of use, about adhesion and the processes in the contact zone between the ceramic and metal as well as about the ceramic-compatible design of the components.
The research work described is funded under grant agreement No. 263476 under the Seventh Framework Program of the European Union FP7 / 2007-2013.
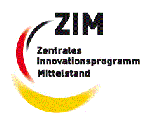
Innoform
The InnoForm project pursued the goal of establishing alternative mould materials, in particular made of ceramics or hard composites, for the non-isothermal blanking of glass components. One of the various areas of application of non-isothermal blanking is the serial production of optical components made of glass, for example to enable the production of inexpensive LED lighting optics, which require particularly good resistance to extreme temperatures and UV radiation. In this segment, the service life of the tools is a critical success factor because it has a direct impact on the unit costs of the stamped glass components. As with all replicative processes, the shape of the die and especially the materials used are of crucial importance.
For non-isothermal blanking, only steel dies have been used so far. However, the limited hardness, strength, temperature resistance and chemical resistance of the steel lead to high wear, to a large repolishing effort and ultimately to the total failure of the die after a comparatively short life cycle.
As part of the project, various ceramics and refractory materials were examined with regard to their suitability for non-isothermal blanking. In this case, alongside considerations for the pure stamping process, also the upstream die construction and the design of ceramic tool systems were specifically considered. A final evaluation of promising material approaches was carried out through stamping tests on a technological scale as well as in small batches, each with 5000 pressing cycles. By employing the best material variants, it was not only possible to achieve a service life that was many times longer than that of the steel dies, but also a significantly increased blank accuracy of P-V = 2 μm with a repeatable accuracy of ± 0.3 μm.
The research work described was funded through the Central Innovation Program for SMEs (ZIM), run by the German Federal Ministry of Economics and Technology (BMWi).
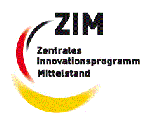
N-ceramic
Carrier substrates made of monocrystalline aluminium nitride (AlN) are ideal for the deposition of semiconducting (AlGaIn) N-layers, which are used, among other things, as a basis for powerful and long-lasting UV light and laser diodes. The great advantages of these components have so far not come into play, however, since single-crystal AlN wafers have so far only been produced through a very complex process and at a high costs at research institutes for their own use. The main reason for this is the lack of a suitable high-temperature and corrosion-resistant crucible material, which would meet both the demanding requirements of the AlN single crystal growth process and the economic requirements.
In the project, therefore, QSIL Ingenieurkeramik GmbH are working together with the Leibniz Institute for Crystal Growth in Berlin on the development of refractory ceramic materials and composite materials as well as of the high-temperature compression techniques necessary for the production, with the aim of developing usable crucible materials and components for the industrial production of single-crystal AlN wafers.
The research work described was funded through the Central Innovation Program for SMEs (ZIM), run by the German Federal Ministry of Economics and Technology (BMWi).
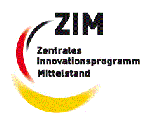
CleanSi
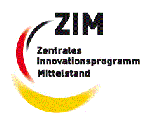
Nitride foam
Within the framework of this project, foam ceramics with adjustable porosity were developed at QSIL as a graphite substitute for growing highly perfect, low-defect AlN single crystals. The work included the development of suitable technologies for the primary shaping of foam preforms, their subsequent sintering as well as experiments to vary the porosity level and structure. The final foams made of tantalum nitride are free of carbon, have a high chemical and thermal stability in the region of 2200°C, and exhibit a relatively high electrical resistance. They were also tested at the IKZ under conditions close to cultivation in order to evaluate the criteria necessary for the planned use of this material as thermal insulation and as a substitute for graphite.

ForNextGen
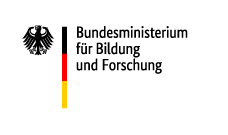
Pades
In aqueous processing, Si3N4 particles react with water. This reaction and the consequences thereof are not desirable. It has a negative effect on the processing options of the powder and on the product properties.
For sintering Si3N4 ceramics, oxidic additives are necessary in order to form a glass phase connecting the silicon nitride crystallites during sintering. The type and amount of additives play a decisive role in determining the properties of the resulting ceramic.
In this project, Si3N4 particles were functionalized by our project partner by applying oxidic additives or their precursors in order to passivate the particle surfaces and to slow down or even completely prevent the reaction with water. Furthermore, the functionalization is expected to improve the homogeneity of the additive distribution. These functionalized powders were processed and examined at QSIL Ingenieurkeramik. Out of the two process routes attempted for functionalization, the one involving “acid hydrolysis” was successful. Using slip casting, it was possible to manufacture test specimens and demonstration items from the obtained powder samples, which sintered densely and exhibited a structure with fewer defects compared to the prior art. The flexural strength measurements of the test specimens made from these functionalized powders were in each case greater than with slip-cast test specimens produced according to the prior art.
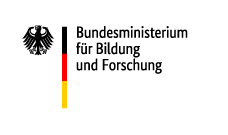
Ultraspan
SinDia
“Development of highly thermally conductive diamond-Si3N4 composites”
When looking at the mechanical properties of materials, some technologies require ceramic materials with high strength, fracture toughness and stiffness. In addition, when looking at the thermal properties, a small to very small coefficient of thermal expansion, the highest possible coefficient of thermal conductivity, good thermal shock behaviour but also high corrosion resistance should all be implemented in order to generate an expanded application potential. Silicon nitride is largely suitable for this, although the intrinsic thermal conductivity reaches a ceiling independently of the sintering additives and compression parameters employed. Materials with a coefficient of thermal conductivity over 100 W/mK usually show a significantly reduced strength and fracture toughness. This is where the novel approach of designing composite materials is supposed to come into play and to lead to a further increase in thermal conductivity. Through the addition of diamonds to a composite material and the development of the corresponding manufacturing process, the aim is to obtain a ceramic material with a significantly higher coefficient of thermal conductivity combined with high strength and a low coefficient of thermal expansion.